3D printing is quickly becoming the rage among both creative makers and industry. The ability to produce three-dimensional parts and items at will is too much to resist. As the cost of setting up and using a 3D printer drops, materials and machines are improving to allow more detail for craftspersons and more rigid tolerances for manufacturing applications. One problem remains.
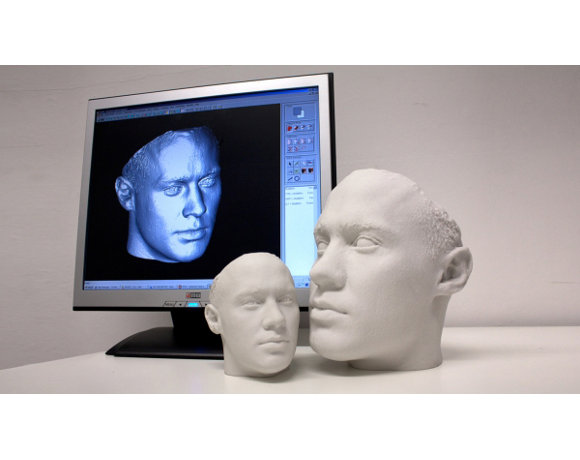
No matter the detail, you are still left with a rigid, plastic or polymer construct. That’s where 4D printing comes in.
4D printing is similar to 3D printing in that you are crafting an item by applying layer upon layer of material. The difference with 4D printing is the job isn’t finished when the printer stops. The fourth dimension represents the ability of the final printed object to change, in some cases even changing itself when conditions are met. That makes it a game-changer.
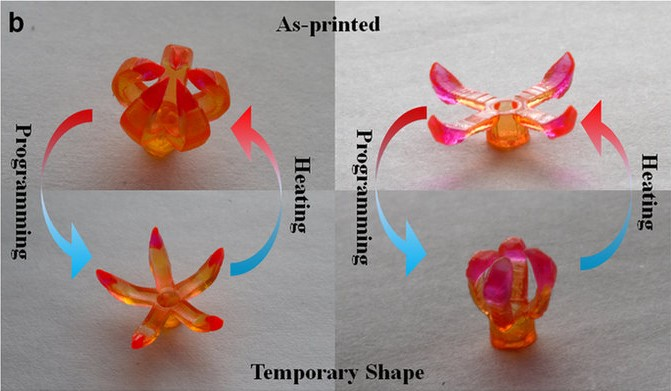
While there are several companies working with the 4D printing concept, the MIT Self-Assembly Lab is widely regarded as the leader of the pack. While right now most of their demonstration pieces look like odd children’s toys, they’re generating a lot of attention from the industry and the government. Recently they were awarded a grant of almost a million dollars by the United States Army to further their efforts and see how far this technology can go.
By creating materials that can be easily printed at a central location then deployed to fulfill their intended purpose, it opens a wide range of possibilities for this new technology:
- Printed clothing that meets specific design needs. Dresses that change color on the red carpet and better armor for our military are both within the realm of possibilities. While the technology is still in its infancy, researchers have already had luck printing dresses made with specialized hinges as part of the process. The result is rigid plastic that drapes like cloth.
- Interactive trade show banners and self-assembling booths. Imagine unpacking a flat, modular booth and using a heat gun to prompt it to self-assemble into the desired configuration. Meanwhile, a banner’s material responds to predetermined stimuli from interested attendants, creating a moving display that generated quality leads.
- Safer pipes for water, oil, and other materials. Pipes that mimic the human intestine to better control flow have already been designed. It is not beyond belief that, in the future, these pipes could be self-sealing along their entire length, allowing for the safer transport of both safe and toxic materials.
- End the housing crisis worldwide. 3D house printing has already happened. In China, a machine was able to make 10 houses in a single day from a mix of cement and construction waste. It is still material and labor intensive, requiring the machine to be at the building site. However, with 4D printing, a structure could be produced, shipped, and then self-assemble on site.
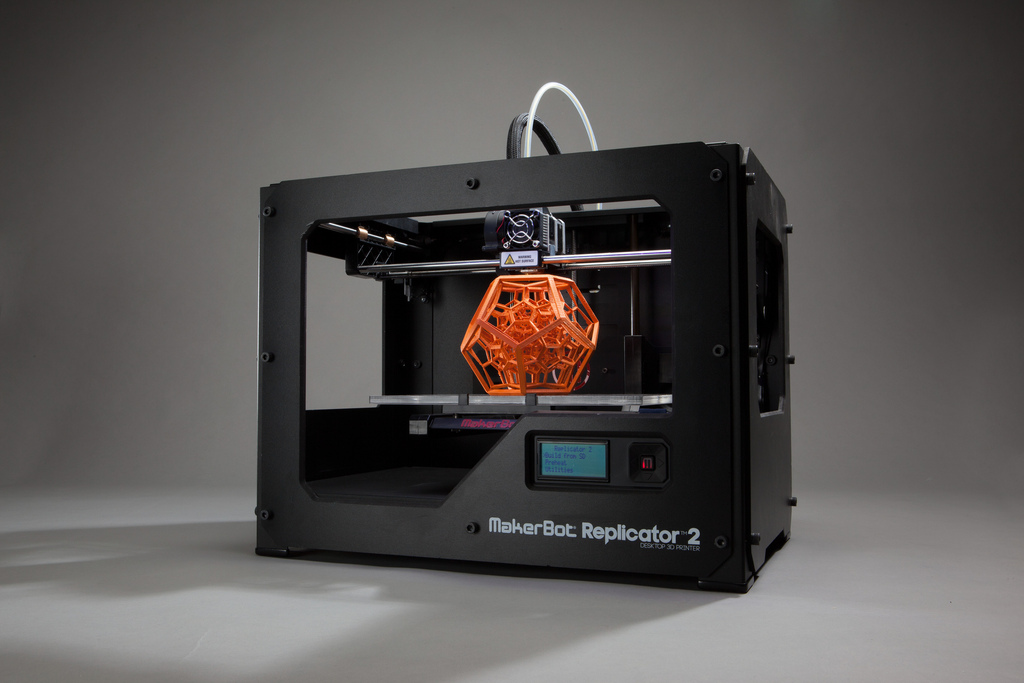
As 3D and 4D printing evolve, expect to see businesses across industry sectors evolve with it. This kind of market disruption has frequently been seen in the digital world, but now the physical world around us is in for some big, exciting changes. Whether you’re talking a static structure or a self-assembling part, the technology is limited only by our imaginations.
Author Bio:
Sean Miller is a freelance blogger based in Ann Arbor, Michigan who has been writing about technology for nearly 10 years. When he’s not investigating the latest in technological innovations and cool gadgetry, he can be found walking his Bloodhound with his wife, Lindsay.
Subscribe to our RSS-feed and follow us on Twitter to stay in touch.
Discover more from Life and Tech Shots Magazine
Subscribe to get the latest posts sent to your email.